Reliable Copper Aluminum Connecting Pipe No Oxide Film During Welding
Place of Origin | Changzhou, China |
---|---|
Brand Name | Yun Neng |
Certification | ISO9001 ISO14001 ISO45001 |
Model Number | 1050 |
Minimum Order Quantity | 3 metric tons |
Price | negotiation |
Packaging Details | Standard export packaging |
Delivery Time | 30 working days after received your down payment |
Payment Terms | T/T |
Supply Ability | 50,000 mt per year |
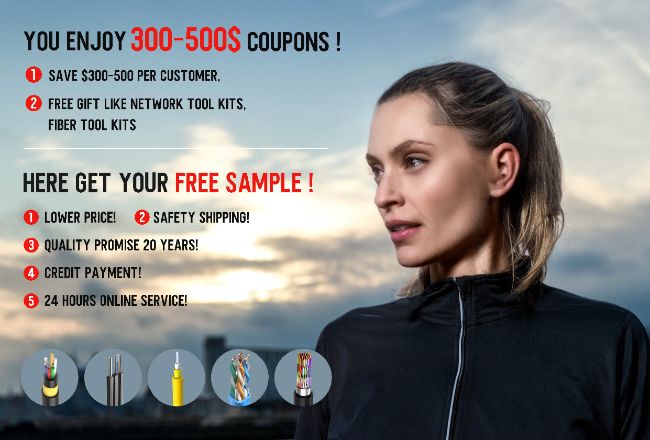
Contact me for free samples and coupons.
Whatsapp:0086 18588475571
Wechat: 0086 18588475571
Skype: sales10@aixton.com
If you have any concern, we provide 24-hour online help.
xFeatures | Anti-corrosion | Product Name | Air Conditioning Connection Pipe |
---|---|---|---|
Model Number | 1050 | State | H14 |
Outside Diameter/mm | 4-22 | Thickness/mm | 0.24-2.00 |
Shape | Coil | Applications | Dehumidifier ,Cold Dry Machine, Warm Air Blower |
High Light | No Oxide Film AC Connection Pipe,22mm Copper Aluminum Connecting Pipe,1050 Copper Aluminum Connecting Pipe |
Reliable Copper-Aluminum Connecting Pipe - No Oxide Film During Welding
Detailed explanation of technical standards for copper-aluminum connecting pipes:
1. Quality requirements for welding points:
The welding joints of copper and aluminum connecting pipes must be free of defects such as pores, cracks, slag, burrs and burns. The two metals, copper and aluminum, should be completely fused during the welding process, with no obvious oxide film. In addition, the size of the plug hole should comply with the standard and cannot be significantly reduced. For example, a Φ6.3 hole should be larger than 3.0mm after plugging.
2. Air tightness requirements:
The air tightness requirements of copper-aluminum connecting pipes are very strict. They need to be tested at a high pressure of 4.0MPa for 5 minutes without any leakage. This is to ensure the stability and reliability of the connecting pipe under high pressure.
3. Pressure resistance performance requirements:
After passing the air tightness inspection, the pressure needs to be slowly increased to 13MPa and maintained for 1 minute. There should be no cracks in the copper-aluminum connecting pipe. This is to test the toughness of the connecting pipe under high pressure and ensure its stability and reliability under high pressure.
4. Bending performance requirements:
The bending performance requirements of copper-aluminum connecting pipes are very high. The sample is bent into a bending core that is twice the nominal diameter of the pipe. After bending 180 degrees, the pipe must not produce wrinkles or cracks. This is to test the flexibility and plasticity of the connecting pipe and ensure its stability and reliability in the bending state.
5. Tensile strength requirements:
The tensile strength of copper-aluminum connecting pipes is required to be between 65-118MPa, the tensile force part is on the side of the aluminum pipe, and the welding seam is above 10mm. This is to test the load-bearing capacity of the connecting pipe and ensure its stability and reliability under tension.
6. Sealing performance requirements:
The sealing performance requirements of copper-aluminum connecting pipes are very high. KTG shrinks well, and the sealing accessories have melted and are completely wrapped in the copper-aluminum joints, and the seal cannot rotate. This is to ensure the sealing and stability of the connecting pipe to prevent leaks and other problems.
Features:
The copper-aluminum air-conditioning connecting pipe is an innovative air-conditioning connecting pipe that tightly combines a section of copper pipe and a section of aluminum pipe through welding technology to form a composite material with excellent performance. This kind of connecting pipe not only has the advantages of high strength, corrosion resistance, lightness, etc., but can also effectively improve the cooling and heating efficiency of the air conditioner. It is a very ideal air conditioner accessory.
First of all, the copper tube part of the copper-aluminum connecting tube can be perfectly connected with the brass parts of the air conditioner's internal and external units, avoiding the risk of electrochemical corrosion between the aluminum tube and the brass parts. Due to the different electrochemical properties of copper and aluminum, the copper-aluminum connecting pipe may undergo electrochemical corrosion in a humid environment, causing holes or cracks inside the connecting pipe, and even causing safety accidents in severe cases. The addition of copper pipes effectively solves this problem and improves the durability and safety of the connecting pipes.
Secondly, the aluminum pipe part of the copper-aluminum connecting pipe can reduce the weight and cost of the connecting pipe, and can also reduce the impact of the connecting pipe on the environment. Aluminum is a lightweight, easy-to-work metal with excellent thermal conductivity properties and is therefore widely used in air conditioning systems. Moreover, aluminum is a renewable metal that will not cause resource shortages or environmental damage, and is in line with the concept of green environmental protection.
Finally, the copper-aluminum connecting pipe as a whole is more insulated than pure aluminum pipes, which can effectively maintain the temperature inside the connecting pipe, reduce the loss of refrigerant during the transportation process, and improve the cooling and heating efficiency of the air conditioner. Due to the high thermal conductivity of aluminum pipes, the thermal insulation performance of pure aluminum pipes is relatively poor, while the copper pipe part of the copper-aluminum connecting pipe has better thermal insulation performance, which can effectively reduce the loss of refrigerant during the transportation process and improve air conditioning. cooling and heating efficiency.
To sum up, the copper-aluminum air conditioning connecting pipe is a very ideal air conditioning accessory. It has the advantages of high strength, corrosion resistance, lightness, and good thermal insulation performance. It can effectively improve the cooling and heating efficiency of the air conditioner and is in line with the environmental protection requirements. idea.
Applications:
evaporimeter
condensator
dehumidifier
Cold dry machine
warm air blower
etc.
Techical Parameters:
Mechanical properties and structure
1, the tensile strength of the bimetallic composite pipe is 150-160MPa, elongation is 35-40%; pressure resistance of 15MPa or more.
2, copper-clad aluminum tube for the integration of materials, copper and aluminum can not be separated, like copper pipe bending, flaring, softness and copper pipe.
3, the section of the pipe contains copper and aluminum weight ratio of 60/40, the pipe outer diameter, wall thickness, specifications and the same as the original copper pipe.
Model Number |
State | Coil | |
Outside Diameter /mm |
Wall Thickness/m m | ||
1050,1060,1070 | M(O) | 4-22 | 0.24-2.00 |
H14 | |||
3003,3103 | M(O) | ||
H12 | |||
H14 |
(Technical requirements refer to national standards or customer technical quality requirements for production)
Support and Services:
We can provide technical support and services for the use of aluminum pipes, including technical guidance, assistance in production, etc. Our experienced technicians can assist you with any problems your product may encounter. We also provide regular after-sales service to ensure that your products are always run at the highest efficiency. We are proud of our work and strive to provide the best customer service.
If you have any questions or concerns about the product or your use, please feel free to contact us. We will always give you the answers you need.
FAQ.:
Q1: aluminum alloy pipe compared with copper pipe, advantages and disadvantages?
A1: Aluminum pipe cost low ductility, but easy to corrosion. Copper pipes have good thermal conductivity and corrosion resistance, but the installation, preservation and transportation are not easy and the cost is high.
Q2: What should be noted in the installation of the air conditioning connection pipe?
A2: The alloy pipe is easy to install, but the link of copper and aluminum after a long time of chemical changes, will cause electrocouple corrosion.
Q3: How to deal with the corrosion problem?
A3: Our products use special corrosion resistant alloy, and the corrosion resistance effect is greatly improved compared with ordinary aluminum alloy. The corrosion resistance experiment is> 1000 hours, which greatly improves the service life of the product.
Q 4: What state and performance of aluminum pipe and aluminum alloy pipe can be produced?
A 4: It can produce performance products from hard state to soft state and interval.